Excavator accessories belong to specialized industry equipment accessories that require specialized equipment for processing and manufacturing in order to operate efficiently and with high quality, such as CNC plasma cutting machines, groove milling machines, rolling machines, welding displacement machines, boring machines, casting (forging) equipment, heat treatment equipment, etc. Excavator accessories may experience wear and tear over time, so how can we reduce wear and tear? Let's take a look together.
Reduce wear and tear on excavator accessories:
1. Preventing corrosion of parts
The corrosive effect on excavator accessories is sometimes difficult to detect and easily overlooked, with greater harm. Rainwater and chemicals in the air infiltrate into the interior of the machinery through pipes, gaps, etc. of mechanical components, corroding them. If the corroded parts continue to work, it will accelerate the wear of the excavator and increase mechanical failures. Operators are required to adopt reasonable construction arrangements based on the local weather conditions and site conditions at the time, in order to minimize the harm of chemical corrosion to mechanical parts.
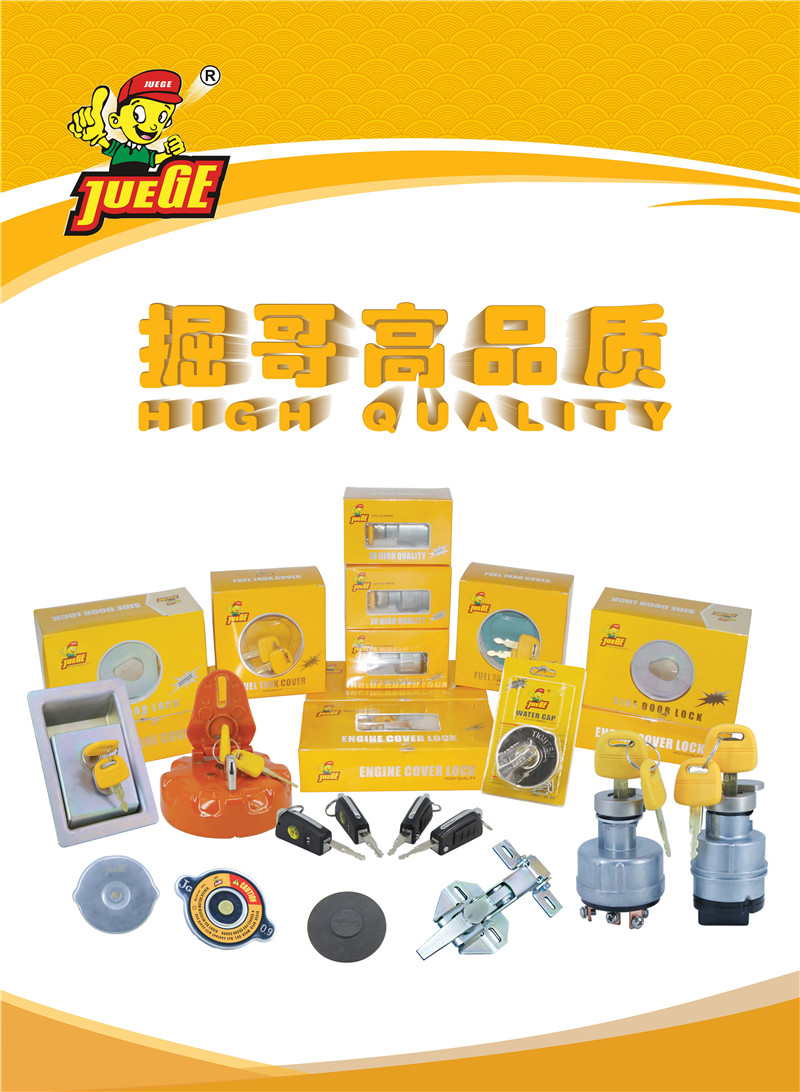
2. Maintain operation at rated load
The nature and size of the working load of excavators have a significant impact on the wear and tear of mechanical components. The wear of excavator accessories generally increases with the increase of load. When the load borne by excavator accessories is higher than the designed working load, their wear will intensify. Under the same conditions, stable loads have less wear on parts, fewer faults, and longer service life compared to high-frequency dynamic loads.
3. Maintain parts at a reasonable temperature
In work, the temperature of each component has its own normal range. Whether the temperature is too high or too low can affect the strength of the parts, so it is necessary to cooperate with coolant and lubricating oil to control the temperature of some parts and make them work within a reasonable temperature range.
4. Timely cleaning to reduce the impact of mechanical impurities
Mechanical impurities usually refer to substances such as dust and soil, as well as certain metal shavings and oil stains generated by construction machinery during use. Impurities that reach between the working surfaces of machinery can damage the lubricating oil film and scratch the mating surface.
Reducing the failure rate of mechanical equipment relies entirely on routine maintenance and timely replacement of vulnerable parts of excavators. I believe that achieving these will definitely reduce the failure rate of excavators and prevent some delays caused by faults. I hope the above content can be helpful to everyone.
Post time: May-18-2023